
NASA held a media event on December 5 to discuss the findings regarding the Artemis 1 Orion heatshield issues that occurred during its reentry after a successful test flight including NASA Administrator Bill Nelson, Deputy Administrator Pam Melroy, Associate Administrator Jim Free, Artemis II Mission Commander Reid Wiseman, and Moon To Mars Program head Amit Kshatriya. Also discussed were updates to the Artemis II Orion crew module’s electrical and life-support systems as the spacecraft is prepared for Artemis II.
Artemis 1 launched on November 16, 2022 from Kennedy Space Center’s LC-39B. During the mission’s 25 days, 10 hours, 53 minutes, SLS sent Orion on a path that saw it go farther than any man-rated spacecraft in the history of spaceflight. On December 11, Orion, using a skip-reentry, reentered the Earth’s atmosphere protected by its 16 foot diameter Avcoat ablative heatshield that hit the atmosphere at 32-times the speed of sound and bore those velocities and heating for over 3,600 miles to land within 2 miles of the USS Portland, its recovery ship. However, there were areas of the Orion heatshield that did not behave as expected during Orion’s reentry back to Earth.


In a tour de force presentation, Amit Kshatriya, NASA’s Deputy Associate Administrator and head of NASA’s Moon to Mars program office gave a presentation on what happened to the Artemis 1 Orion’s heatsheild and the steps taken to understand why. As he said, an ablative heatshield like Orion’s is designed to burn, or char, during reentry. Most of the heat of reentry is removed by what NASA calls the “radiative shock” that occurs in front of the spacecraft as it travels through the atmosphere. The rest of the heat of reentry is removed by convection through charing of the heatshieldt’s outer layer. This char layer of the ablator on the heatshield is designed to gradually recede, or burn-away, so that the material underneath protects the spacecraft during the high heat experienced during reentry. The heatshield is not designed for areas that are charring to break-off, as happened during reentry of the Artemis 1 Orion spacecraft. There were about 100 areas of Orion’s heatshield where the char layer that protects Orion broke-off in ways that NASA had not expected.


The Orion heatshield had excellent performance, according to NASA. But unlike periods in the past that led to the loss of the Challenger and Columbia crews, according to Kshatriya, NASA of today doesn’t think of unexpected behavior of something so critical as a heatshield means that it’s still behaving within margin. NASA decided it was imperative to get a full technical understanding of the “transported liberation phenomena”, as NASA calls it, that led to the loss of char.
According to Mr. Kshatriya, the Orion program head, Howard Hu, stood-up a heatshield tiger team run by Johnson Space Center’s Luis Saucedo that was a multi-disciplinary group consisting of thermal protection systems, aerothermal dynamics, aerothermal testing analysis, thermal testing analysis, stress analysis, material testing, with additional experts brought-in from the Department of Defense, Department of Energy, across industries and countries. According to Kshatriya, “…Saucedo…conducted what is in my estimation in the 20-years I’ve been in the agency is one of the most magnificent pieces of engineering analysis that I have been a part of. Their work was substantial, significant, and extremely impressive.” The Orion heatshield tiger team, “…led to advances enabling an understanding of Orion’s heatshield material loss properties and its interaction in the aerothermal environment, created new technologies test and non-destructive evaluation techniques to observe the heatshield’s aerothermal environment interactions in NASA’s arc jet facilities, which were upgraded as part of this work.”
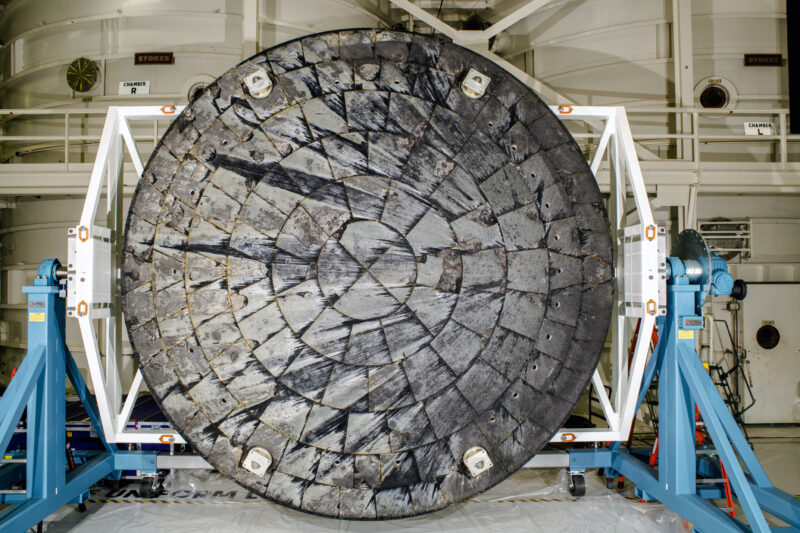
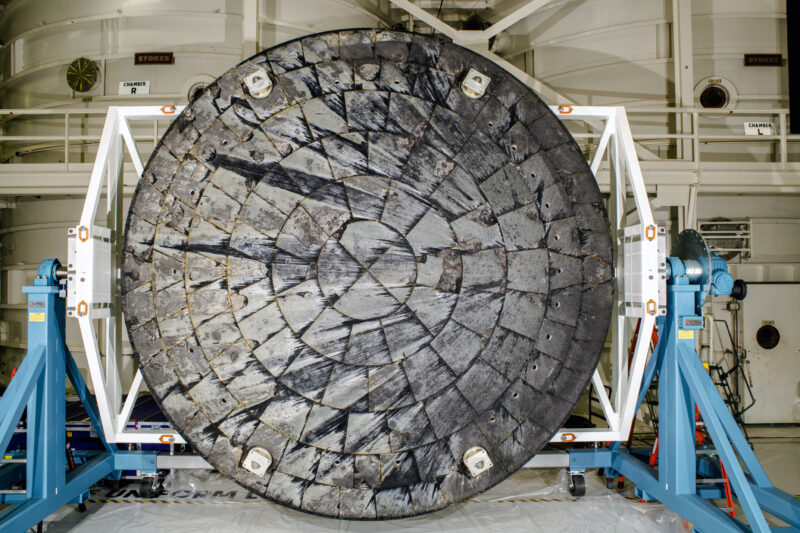
Once the Orion heatshield tiger team’s report was completed, a full verification was done by an outside group, led by Paul Hill, who is also a key advisor serving on the Aerospace Safety Advisory panel, that was made-up of experts brought-in from across industry both US and international. The intent was give NASA confidence that it truly understood the unexpected behavior of Artemis 1’s Orion heatshield during reentry. This group was unanimous in its agreement of the analysis as to the root causes of the Orion heatshield’s behavior.
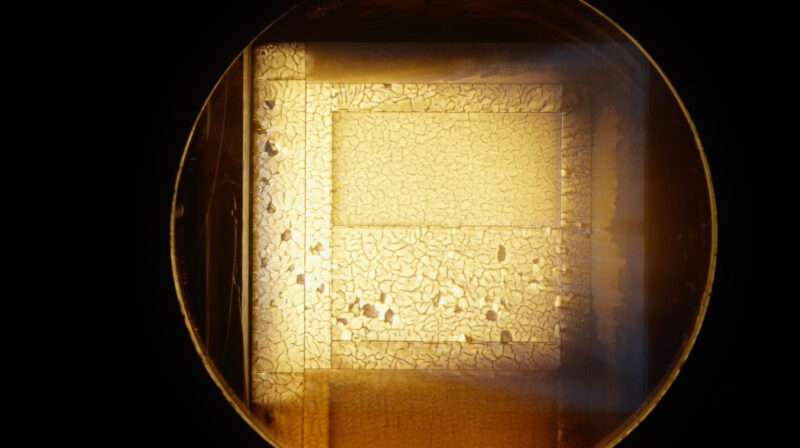
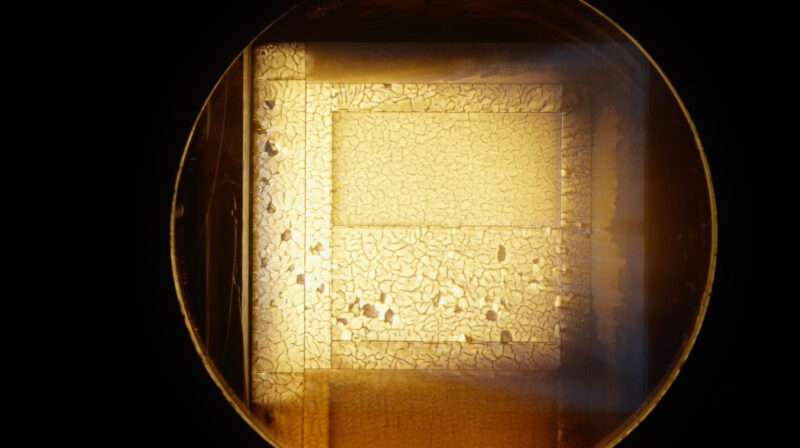
During reentry, the ablative material has to produce gases under pyrolysis, that is burning away of material in a high thermal environment without oxygen. As Kchatriya said, NASA learned that as part of that reaction, the permeability of the Avcoat heatshield material is critical. The insight into what happened did not come until NASA looked at regions of the the Avcoat material where the burning-away of the char layer stopped during the dwell-time of the skip reentry, that is the period of the skip reentry during which Orion was experiencing less thermal loading. During this period, the production of gases from the Avcoat material was higher than the permeability, which is the ability of the material to allow flow of gases, allowed. The increased pressure due to the higher production of gases within the Avcoat material that could not readily escape because of the material’s permeability led to a difference in pressure that resulted in cracks “in plane with the outer mold line” of the Orion crew module. In some cases, those cracks made their way all the way to the bond-line, or where some of the 186 Avcoat heatshield meet other blocks.
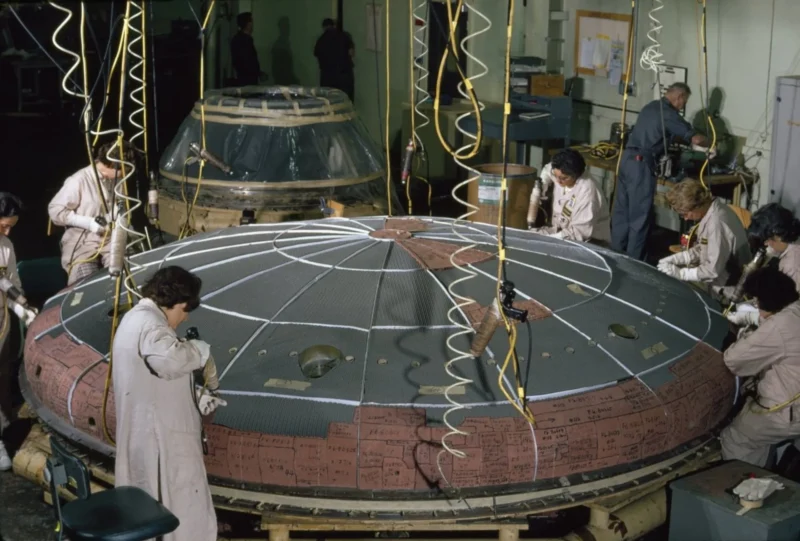
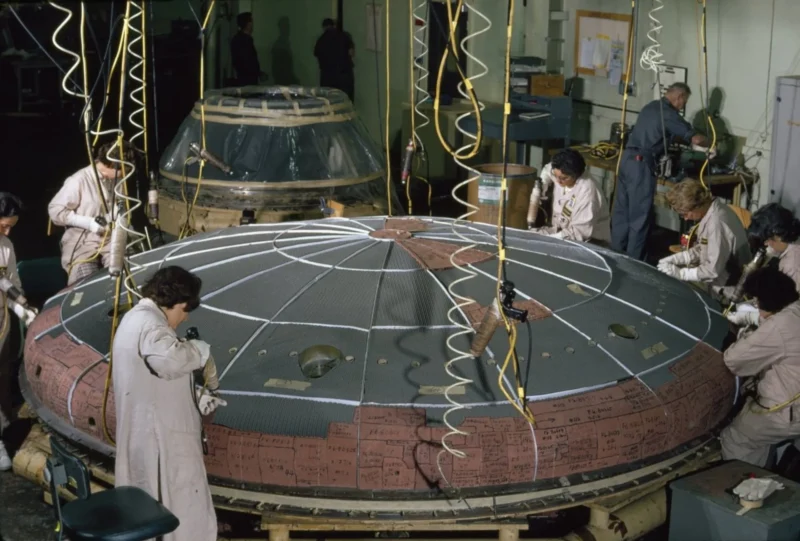
One question on many people’s minds is why the Apollo command module heatshield, as well as the EFT-1 Orion crew module’s heatshield, did not experience Avcoat issues. The heatshields of these spacecraft incorporated Avcoat hand-filled in a honeycomb structure. Containing the Avcoat material within honeycomb cells abbreviated propagation of any crack propagations from progressing beyond each honeycomb cell. But the cost of a heatshield built by hand is expensive and prone to its own errors, such as voids from incomplete fills. There is also the mass penalty of the honeycomb structure itself. NASA’s current Orion heatshield design employing Avcoat brick is meant to win-back that honeycomb mass and be able to produce massive Orion spacecraft heatshields on a less expensive and more rapid manner.
Because of the Orion heatshield test program, NASA now knows how to produce Avcoat with the needed permeability standards and has, according to Kshatriya, sized-up production capability resulting in a 50% jump in the production rate to quickly produce Avcoat heatshields at a rate NASA needs. NASA thinks the qualification of the reformulated Avcoat will be completed within a year. In the meantime, since NASA fully understands, “…not only the interaction of the Avcoat material and the environment but also the integrated interaction of how it performs on the spacecraft,” NASA is going to fly the current heatshield on the Artemis 2 Orion spacecraft because it feels that there’s no better way to learn than to fly.


The current Artemis 2 Orion heatshield has a similar Avcoat formulation to Artemis 1’s Orion. There are two ways to prevent the Avcoat heatshield issues that occurred during Artemis 1 Orion’s reentry: change-out the Artemis 2 Orion heatshield with one using the newly formulated Avcoat blocks; or change the reentry environment. NASA has chosen the latter option, that is to change the reentry environment. Because NASA is using an equatorial free-return trajectory to send the Artemis 2 astronauts to the Moon, it can control the reentry environment and do so safely and has chosen this path in order to continue to move the Artemis 2 program forward. Artemis 2 Mission Commander Reid Wiseman stated that the Artemis 2 crew is fully behind NASA’s decision.
Making the needed changes to the Artemis 2 mission’s reentry guidance, along with resolving a handful of issues in the performance and integration of the Orion spacecraft, will delay the September 2025 launch of Artemis 2 to April 2026. There are issues with the electrical system of the Orion spacecraft during an abort.
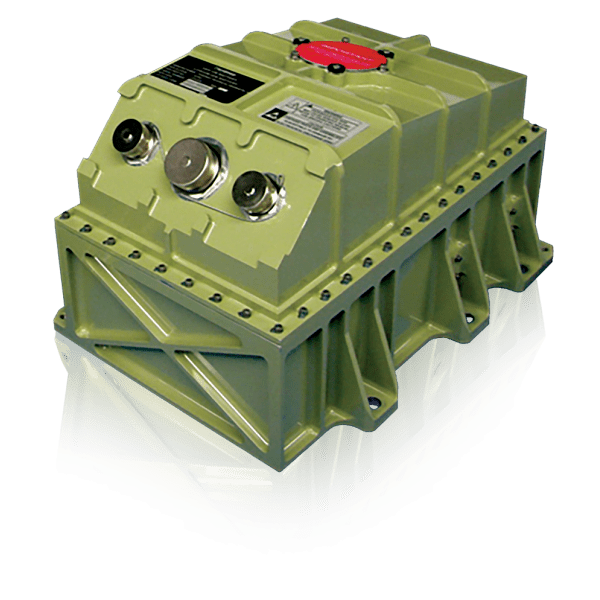
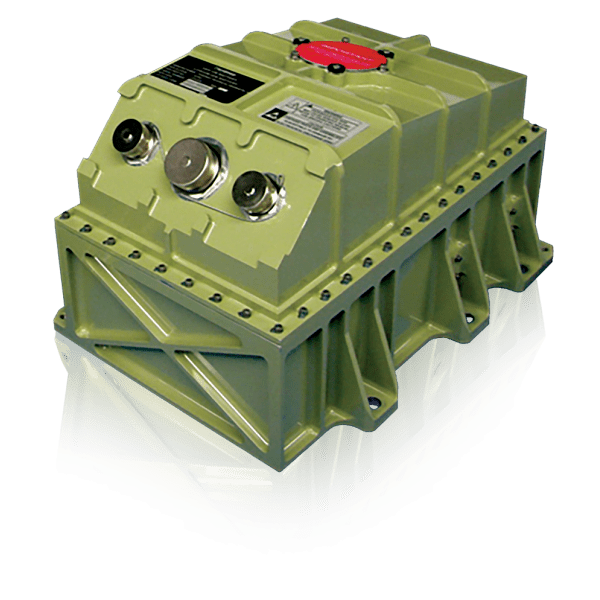
It was discovered that the two primary and two back-up EaglePicher 120-volt Li-ion batteries on the Orion spacecraft, which are responsible for communications, navigation, propulsion and thermal control, were not, as explained by Dep. Assoc. Admin. Kshatriya, able to tolerate the intense environment experienced during an abort using the launch abort system. Each of the 120-volt Li-ion batteries, according to EaglePicher, contain 32 EaglePicher 30 Ah prismatic, lithium-ion cells. Since all of the abort systems on the Orion spacecraft, including the launch abort system, will be active on Artemis 2, NASA has been working to make sure that all of the electrical system issues during abort are resolved. Fixing the batteries has taken some time and involved a complete rework in how the batteries are mounted and mechanically secured in the Orion spacecraft. Kshatriya called-out the excellent work by EaglePicher Technologies in Joplin, Missouri, the supplier of the Orion spacecraft batteries, enabled the complete and quality to fix. Remedying the battery fix was made difficult in finding very high reliability components due to the extreme fragile nature of the space components supply chain. Interestingly, Kshatriya mentioned that NASA has a long history with EaglePicher and that its batteries were the ones that saved the Apollo 13 crew once the fuel cells were lost. After the Apollo 13 command module was shut-down, it and its EaglePicher batteries spend days being cold-soaked in space. Because the Apollo 13 batteries could be powered-up, the Apollo 13 crew was able to successfully reenter and splash-down.
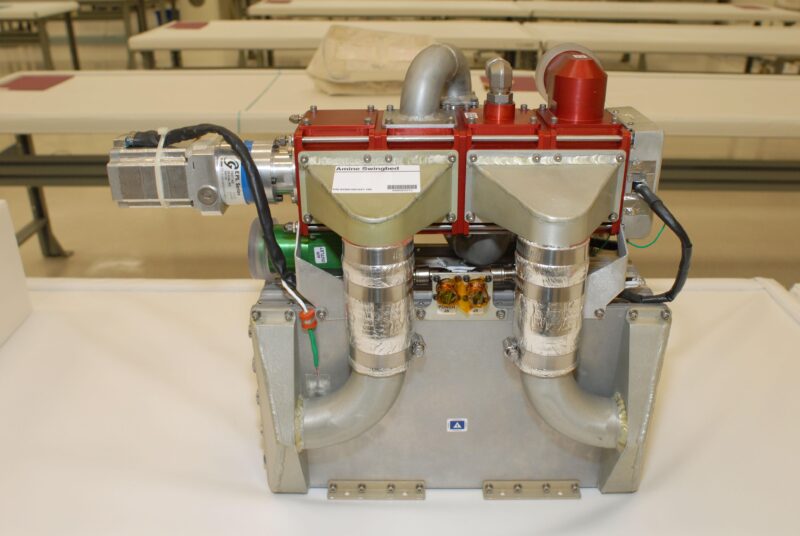
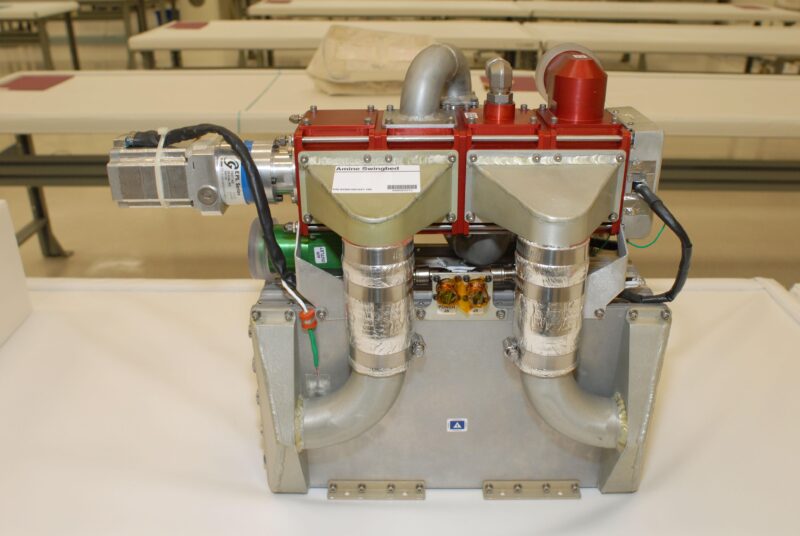
Resolving issues with the Orion Environment Control Life-Support System (ECLSS) has taken longer than planned. An issue was announced in early 2024 in the ECLSS involving the control system of the valves for the carbon dioxide removal system. Another ECLSS issue was the sealing material on the valves being deformed and causing over-board leakage. Both of these ECLSS issues have been fixed. NASA continues to test the Orion ECLSS through multiple failure paths, to in essence beat it hard, to ensure that it will work as needed for the Artemis 2 and future crews. Since all of the issues regarding Orion’s batteries, ECLSS, and heatshield have been resolved, NASA has decided to go forward with stacking the Artemis 2 launch vehicle and Orion spacecraft.
NASA is using the time until the spring 2026 launch of the Artemis 2 mission to work with its commercial partners to retire risk for the Artemis 3 landing mission, should SpaceX’s Starship be ready.